How Expert Packaging Maker Repair Provider Reduce Downtime and Increase Efficiency
In today's competitive landscape, the efficiency of packaging operations is extremely important for maintaining an effective service. Specialist product packaging maker repair services are essential in decreasing downtime and enhancing performance with specialized diagnostics and prompt treatments. By implementing precautionary upkeep techniques, these solutions not only avert expensive failures but additionally ensure regular item quality and process. The implications of such services extend past immediate repairs-- unloading the more comprehensive influence on operational effectiveness discloses essential insights into long-term efficiency methods. The question remains: exactly how can organizations leverage these solutions to accomplish lasting development?
Importance of Timely Repair Works
Prompt repair services of packaging devices are vital for keeping functional effectiveness in any production setting. When equipment malfunctions or breaks down, it can lead to significant disruptions in assembly line, leading to enhanced downtime and shed earnings. The longer a product packaging machine stays out of order, the better the effect on overall productivity, possibly creating delays in meeting orders and reducing client contentment.
In addition to the prompt economic ramifications, delayed fixings can cause extra considerable damages to the equipment. Parts that are not resolved promptly can wear away additionally, needing even more costly fixings or complete replacements, which could have been prevented with timely treatment. Routine upkeep and prompt repairs can improve the life-span of packaging equipments, guaranteeing that they run at ideal efficiency levels.
Buying specialist packaging device fixing services is crucial for minimizing these risks. A positive method to fixings not just keeps production schedules but likewise promotes a society of dependability within the organization. By focusing on prompt repairs, services can maintain their affordable side, maximize resource allowance, and eventually improve their lower line via improved operational performance.
Expertise in Diagnostics
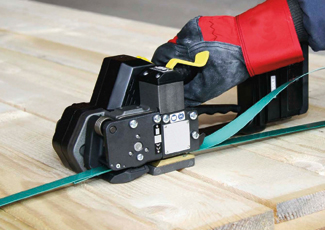
Reliable diagnostics not just help with swift identification of troubles however also boost the overall reliability of product packaging procedures. By carrying out extensive assessments, professionals can examine the health and wellness of critical parts, guaranteeing that also small irregularities are resolved quickly. This attention to information reduces the danger of unexpected malfunctions, which can lead to costly downtime.
In addition, expert diagnostics offer beneficial insights right into functional trends, enabling companies to make enlightened choices pertaining to tools upgrades or adjustments. By leveraging these insights, firms can optimize their packaging processes, bring about improved effectiveness and performance. Ultimately, spending in analysis experience is important for companies seeking to keep seamless operations and promote high requirements of top quality in their product packaging procedures.
Preventive Upkeep Conveniences
Preventive upkeep matches specialist diagnostics by proactively dealing with prospective issues before they materialize into severe troubles. By implementing an organized preventive maintenance program, firms can substantially reduce the danger of unforeseen machine failures, consequently reducing costly downtime. Routine Discover More examinations, cleansing, and parts replacement help make sure that packaging equipment runs at optimal effectiveness.
Among the crucial advantages of preventive upkeep is its capacity to expand the lifespan of equipment. By consistently keeping equipment, organizations can prevent the compounding results of damage that commonly lead to significant fixings or replacements. packaging machine repair service. This not just conserves funding yet also enhances the total reliability of manufacturing procedures
Additionally, preventative maintenance adds to boosted safety problems within the work environment. By determining and rectifying potential find threats prior to they intensify, organizations produce a more secure environment for their employees. This aggressive approach not only shields workers however also cultivates a society of responsibility and alertness.

Customized Solution Solutions
Identifying the unique demands of each service, personalized solution options for packaging machine repair work deal customized methods that boost operational efficiency. These solutions are designed to address certain obstacles dealt with by different markets, making certain that equipment downtime is minimized and efficiency is taken full advantage of.
Expert repair solutions begin with an extensive assessment of a business's packaging operations. By understanding the certain machinery involved and the needs of the production setting, technicians can develop an individualized repair and maintenance plan. This might include specialized training for in-house personnel, the application of predictive maintenance innovations, or the arrangement of dedicated assistance during optimal manufacturing times.
Moreover, personalized solutions can include adaptable service arrangements that line up with a company's operational timetable, enabling repairs to be executed during off-peak hours. By focusing on the distinct requirements of each organization, these bespoke remedies guarantee that fixings are not only effective yet also flawlessly integrate into existing operations.
Eventually, the concentrate on customization allows firms to maximize their packaging procedures, leading to improved reliability and efficiency of machinery, which is important for preserving competitive advantage in today's hectic market.
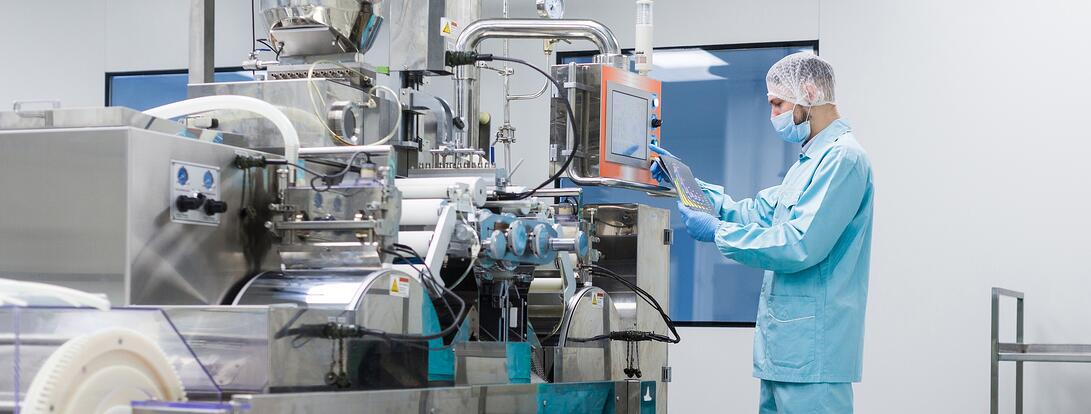
Effect on Total Efficiency
Customized solution remedies not just address certain repair demands yet additionally play a significant function in enhancing total functional performance. By giving targeted treatments, expert packaging device repair work services directly decrease the regularity and period of tools failings. This proactive strategy ensures that assembly line stay functional, minimizing disruptions that can lead to pricey downtime.
Additionally, effective repair service solutions add to smoother operations, as well-kept equipment operates at optimum efficiency levels. When makers work properly, the high quality of packaged items enhances, causing fewer issues and less rework. This enhancement not just enhances efficiency but additionally enhances customer fulfillment.
In addition, regular upkeep and quick reaction times from repair service experts cultivate a culture of reliability within the organization. Workers can focus on their key jobs instead than bothering with possible tools malfunctions. As a result, the general throughput of the manufacturing process rises, enabling firms to fulfill demand better.
Eventually, the tactical financial investment in specialist repair services translates to improved performance across all functional elements, guaranteeing that organizations can adapt and grow in an open market. This synergy between upkeep and performance is essential for long-lasting success.
Verdict
In his explanation conclusion, professional product packaging device fixing solutions play a vital function in reducing downtime and improving efficiency within producing atmospheres. Prompt fixings, specialist diagnostics, and preventive upkeep add to the dependability of equipment, while tailored solution options attend to certain operational requirements - packaging machine repair service.
Comments on “Stay prepared with a dependable packaging machine repair service now.”